A Comprehensive Overview to Welding Inspection: Understanding Specifications, Techniques, and Finest Practices for Quality Assurance

Welding assessment plays a crucial duty in guaranteeing the structural integrity and security of welded elements, requiring a complete understanding of sector requirements such as those developed by AWS and ASME. As we discover these essential aspects, it comes to be apparent that the ramifications of welding examination expand far beyond conformity, inviting a better exam of exactly how these processes form sector criteria and techniques.
Value of Welding Evaluation
Welding inspection plays a critical duty in making certain the integrity and security of welded structures. It is a crucial procedure that confirms that welds comply with predefined specs, which is essential in numerous industries, including construction, auto, and aerospace. By conducting complete examinations, possible flaws such as splits, incomplete combination, and porosity can be determined early, preventing catastrophic failures that could cause accidents or expensive fixings.
The importance of welding examination prolongs beyond mere conformity with policies; it likewise cultivates trust with stakeholders. Customers and regulative bodies expect guarantee that the structures they count on are developed to hold up against operational tensions. Reliable welding assessment techniques add to long-lasting longevity and performance of the frameworks, ultimately leading to decreased upkeep expenses.
Furthermore, welding assessment advertises a culture of top quality within companies, motivating adherence to best methods and constant improvement. By integrating assessment processes right into the welding workflow, firms can boost their credibility and develop themselves as leaders in high quality guarantee. Finally, the relevance of welding assessment depends on its capacity to secure lives, ensure structural integrity, and support market requirements, making it an important aspect of welding procedures.
Key Market Specifications
Making certain compliance with vital industry standards is important for keeping the top quality and safety and security of welded structures. Various companies develop these standards to advertise best techniques in welding and evaluation. Among one of the most identified are the American Welding Culture (AWS) and the American Society of Mechanical Engineers (ASME), which provide in-depth standards and specifications for welding processes and evaluation requirements.
AWS standards, such as AWS D1.1 for architectural welding, summary demands for products, design, and testing to make sure the honesty of welds. In a similar way, ASME codes, including ASME Area IX, govern the qualification of welders and welding treatments, making certain constant high quality in industrial applications. Internationally, the ISO 3834 standard emphasizes high quality needs for fusion welding, offering a framework for companies to show compliance with international finest methods.
Conformity with these requirements not only boosts the reliability of welded frameworks but likewise minimizes threats connected with structural failures. In addition, adherence to industry standards is commonly a requirement for governing authorizations and can substantially influence job requirements. Eventually, understanding and carrying out these essential criteria are important for reliable welding examination and top quality assurance.
Evaluation Techniques Review
Efficient welding assessment relies upon a variety of strategies created to assess the quality and stability of welds. These techniques can be extensively categorized into non-destructive and harmful testing (NDT) approaches. Non-destructive testing methods, which are commonly favored in the market, enable the assessment of welds without jeopardizing the stability of the product.
Among the most frequently made use of NDT strategies are aesthetic inspection, ultrasonic testing, radiographic screening, and magnetic particle testing. Visual inspection is often the first action in the assessment procedure, making it possible for inspectors to determine surface area imperfections and evaluate weld bead accounts. Ultrasonic testing utilizes high-frequency sound waves to discover internal imperfections and determine the density of welds. Radiographic testing entails using X-ray this post or gamma-ray imaging to reveal inner flaws, while magnetic bit screening works for spotting surface area try this web-site and near-surface gaps in ferromagnetic materials.
Each method has its very own benefits and restrictions, making it crucial for inspectors to choose one of the most suitable technique based on the specific requirements of the job, the products involved, and the urgency of the welds being evaluated. This mindful selection maintains and guarantees detailed assessments security and high quality standards in welding operations.
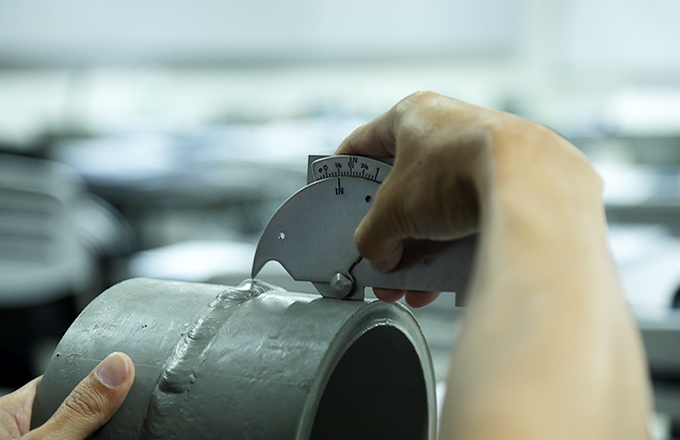
Typical Issues and Their Ramifications
A comprehensive understanding of usual flaws in welds is critical for maintaining structural stability and safety and security in welded constructions. Welding issues can substantially endanger the mechanical homes of the joint, leading to failings that might jeopardize both employees and tools.
Common flaws consist of porosity, which manifests as small gas pockets entraped in the weld steel, damaging the overall framework. Breaking is another common concern, typically resulting from fast air conditioning or incorrect joint design, causing tension focus that can lead to devastating failings. Incomplete blend occurs when the weld metal fails to correctly bond with the base product, developing weak factors that may cause splitting up under lots.
Various other noteworthy issues consist of undercutting, where the weld grain deteriorates the base metal, and slag incorporations, which can hinder the weld's toughness. Each of these issues has certain ramifications; for example, porosity can minimize ductility, while splitting directly influences tensile stamina. Determining and recognizing these defects during inspection is vital for carrying out rehabilitative actions and guaranteeing conformity with sector requirements, eventually safeguarding the architectural stability of welded assemblies.
Ideal Practices for Quality Control
Executing best methods for quality control in welding procedures is important for achieving optimum results and minimizing issues. One essential method is the facility of clear welding procedures that comply with sector requirements and specs. These procedures ought to include thorough guidelines concerning product option, joint preparation, and welding methods to make certain consistency and top quality.
Normal training and qualification of welding employees are additionally important. Experienced welders that comprehend the importance of quality control are most likely to create sound welds. link Furthermore, applying a durable evaluation program, including both non-destructive and visual testing (NDT), can assist recognize problems early at the same time, permitting timely corrective activities.
Paperwork plays a key duty in quality control. Preserving precise records of welding parameters, repair services, and evaluations makes certain traceability and accountability. Utilizing innovative modern technologies such as automated welding equipments can boost precision and minimize the potential for human mistake.
Last but not least, cultivating a culture of top quality within the organization motivates employees to focus on top quality in their job. By adhering to these best methods, organizations can improve the stability of their welding procedures, inevitably bring about boosted product quality and minimized costs associated with rework and repairs.
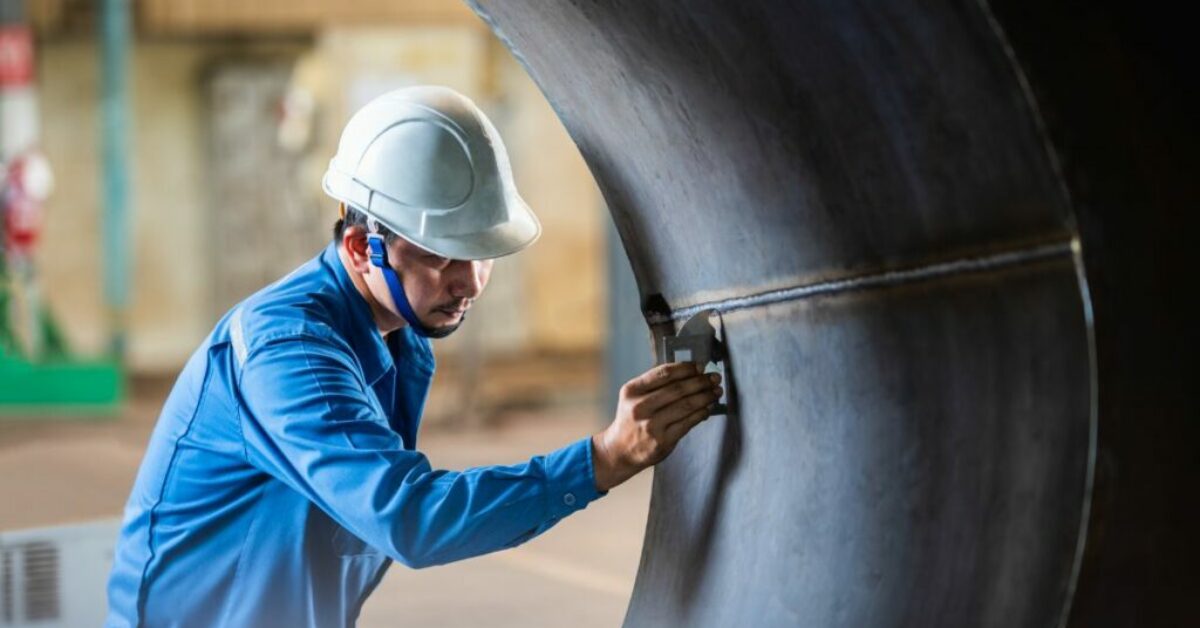
Verdict
To conclude, welding assessment plays an important role in guaranteeing the integrity and security of bonded structures. Adherence to essential industry criteria, such as those established by AWS and ASME, is vital for reliable top quality guarantee. Utilizing various evaluation methods permits the recognition of usual flaws, thereby alleviating possible risks. By carrying out finest methods, organizations can improve integrity, decrease upkeep expenses, and grow trust fund amongst clients, eventually adding to successful welding operations.
Additionally, welding evaluation advertises a society of top quality within companies, urging adherence to best practices and continuous improvement. In conclusion, the value of welding inspection exists in its capability to secure lives, guarantee structural dependability, and copyright industry criteria, making it a vital aspect of welding procedures.
Amongst the most acknowledged are the American Welding Society (AWS) and the American Culture of Mechanical Engineers (ASME), which give thorough guidelines and specs for welding procedures and inspection requirements.
Eventually, understanding and carrying out these vital requirements are important for efficient welding assessment and quality guarantee.
Efficient welding assessment depends on a variety of methods created to examine the quality and honesty of welds. - Welding Inspection Gilbert Arizona